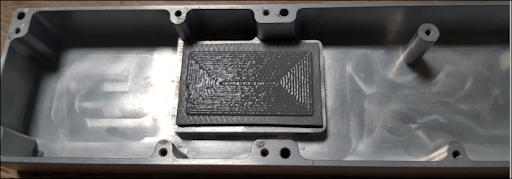
Publié le 2 septembre 2020
La plupart du temps, l’utilisation d’un thermal pad en tant que drain thermique représente la solution idéale pour combler cet espace entre le dissipateur et les composants électroniques et ainsi favoriser la dissipation de la chaleur générée par les composants. Pour qu’il assure correctement sa fonction, le thermal pad doit être compressé, généralement de l’ordre de 15 à 40%. Les forces de compression exercées sur le thermal pad sont directement subies par la carte électronique (PCB) , pouvant aller jusqu’à générer un flambage du PCB (déformation mécanique liée à une force exercée). Cette déformation mécanique du PCB peut entraîner le dessoudage de certains composants sensibles, plus précisément sur les composants à billes de type BGA.
Pour limiter cette force de compression, tout en assurant la liaison thermique entre des composants de différentes hauteurs et un dissipateur, il est possible de recourir aux gels thermiques également appelés pâtes thermiques ou gap fillers . Cette solution consiste à poser une pâte thermo-conductrice en recouvrement des composants à dissiper, en quantité suffisante pour assurer le contact mécanique avec le dissipateur. Néanmoins, cette méthode présente elle aussi certaines contraintes. En effet, la technique de pose nécessite une machine spécifique pouvant être un investissement coûteux.
Afin de répondre à cette problématique de plus en plus répandue à laquelle aucune des deux solutions ne satisfait pleinement, dB & Degrees a conçu un produit novateur : le DG-STACK.
Les principes d’utilisation du Thermal Pad
Le Thermal Pad est un polymère chargé de particules caloporteuses qui, par compression, assure le transfert de la chaleur d’une source chaude vers un dissipateur. Les pads, plus communément appelés les interfaces ou matelas thermiques, se dimensionnement par une épaisseur nominale, des dimensions XY, une dureté shore, une conductivité et/ou une résistance thermique ainsi qu’une compression à exercer.
La dépose s’effectue manuellement la plupart du temps. En règle générale, un matériau peu performant / peu conducteur thermique est souple et facile à comprimer (1 à 5W/m.K), alors que les matériaux plus performants (6 à 32W/m.K) sont souvent plus durs.
Avantages du thermal pad
Les avantages du Thermal Pad sont nombreux :
- Manipulation aisée à la main
- Très faible coût d’outillage de découpe lorsqu’un outil et nécessaire
- Bonne tenue à la vibration
- Possibilité d’avoir une ou deux faces non collantes
- Remplacement facilité en cas de maintenance
Inconvénients du thermal pad
Sur les produits performants thermiquement, la compression du thermal pad nécessite des efforts mécaniques importants. Ces efforts sont alors subis par la carte électronique (phénomène de flambage). Ceci peut dessouder certains composants fragiles, comme les composants à billes par exemple. Ceci est encore plus vrai sur une carte électronique disposant de plusieurs composants de différentes hauteurs à relier à un dissipateur commun. Il faudra dans ce contexte prévoir plusieurs épaisseurs de thermal pads (gestion de plusieurs références articles), pour compenser toutes les différences de hauteurs de composants et assurer un contact mécanique avec le dissipateur sans générer de flambage de la carte électronique. Cette diversité de thermal pads de différentes hauteurs peut, dans certain cas, engendrer des pertes matières lors de la phase de découpe des plaques de thermal pads, et un coût de production nécessairement augmenté.
Les principes d’utilisation du Gap Filler
Appelé également pâte thermique, le Gap Filler est un matériau polymère pâteux mono ou bi-composants, qui se dépose par automate. Il peut également se déposer au pistolet manuel pour des retouches ou des faibles quantités en production. Il présente l’avantage majeur d’être très facilement compressible : il nécessite très peu d’efforts de compression. Le Gap Filler peut remplir des espaces de 1 à 5 mm, se déposer sur différentes hauteurs de composants disposés sur une même carte, couvrir une surface en déposant un cordon de matière ou par plots etc…
Avantages du gap filler
La consistance pâteuse de la matière (du type gel dentifrice) permet d’assurer une liaison thermique parfaite entre le composant et le dissipateur avec un effort de compression négligeable. La pâte peut être déposée à différents endroits de la carte, sur différentes épaisseurs… à partir d’un seul et unique programme de dépose. La quantité de matière à déposer correspond exclusivement à la quantité nécessaire, ce qui limite les pertes. Le conditionnement en seringues, en cartouches, ou en barils permet de s’adapter parfaitement aux cadences de production. En outre le gap filler permet de rattraper des tolérances min /max très importantes.
Inconvénients du gap filler
Lorsqu’il est déposé par automate, le gap filler nécessite un dispositif de dépose automatique (robot) . Lorsque la dépose de pâte s’effectue par un sous-traitant, et non sur votre ligne de production, ce procédé nécessite une logistique complexe liée à l’envoi des pièces mécaniques (dissipateurs par exemple) sur lesquelles sera déposée la pâte. Qui plus est, il peut y avoir une incertitude de la bonne tenue du dépôt de pâte dans le transport : en position verticale durant une durée prolongée, la pâte peut être amenée à légèrement glisser dans certains contextes (chocs, vibrations…). Enfin, une fois déposé sur la mécanique ou sur la carte électronique, le gap filler ne peut pas se manipuler directement à la main sans altérer sa géométrie de dépose.
La solution unique dB & DEGREES : le DG-STACK
Pour répondre aux problèmes de flambage des cartes électroniques tout en résolvant le besoin de dissipation thermique, dB & DEGREES a mis au point le DG-STACK, une solution hybride qui consiste à combiner une dépose de gap filler directement sur un thermal pad de très fine épaisseur.
(illustration dépose FIP sur une plaque de matière découpée en 55x25mm / déposes FIP de différentes hauteurs sur différentes formes de pads afin de faire un KIT).
Principe et utilisation du DG-STACK
Ainsi, le fabricant peut continuer à commander des thermal pads et à les déposer manuellement mais il aura bénéficié des avantages de manipulation du thermal pad ainsi que des avantages de contraintes mécaniques du gap filler. Un packaging adapté est alors proposé pour assurer un transport dans de bonnes conditions et une préhension aisée de la pièce lors de l’intégration dans l’équipement.
Le DG-STACK directement appliqué sur une pièce mécanique, restera parfaitement maintenu sur la surface métallique grâce à la nature collante du thermal Pad (TACKY) quelle que soit son épaisseur. Le Gap filler déposé préalablement sur le pad sera solidaire chimiquement et sera ainsi retenu, limitant tout risque de fluage par gravité durant le transport, même en position verticale et soumis à des vibrations.
Quelle que soit la géométrie, il est donc possible de mettre en œuvre cette solution et ainsi d’assurer une continuité thermique sans exercer de pression excessive sur vos composants électroniques.
Pour chaque cas client, nous prenons en compte les espaces à combler et les jeux de tolérances mécaniques des composants et des mécaniques à mettre en contact avec ces composants. De ce constat, nous identifions et adaptons la hauteur de pad thermique nécessaire et la hauteur de gap filler la plus adaptée. La solution est sur-mesure, optimisée mécaniquement et thermiquement, pour ne pas faire flamber mécaniquement la carte électronique et ne pas détériorer ni les composants électroniques ni leurs points de soudure sur la carte électronique, et pour garantir la bonne dissipation de la chaleur des composants électroniques
Notre solution DG-STACK est disponible en deux versions :
Ainsi, le DG-STACK nous permet de proposer une solution unique pour assurer une liaison thermique optimale avec le dissipateur. Avec ce procédé, le gap filler va se répartir autour des composants et encaisser les variations de hauteur de chacun d’entre eux. Grâce à ses propriétés, le gap filler exercera une pression suffisante sur le thermal pad pour assurer sa compression et son efficacité thermique. Cette solution innovante permet de bénéficier d’une technologie de pointe sans la nécessité d’outillage, d’investissement machine et de compétences autrefois indispensables.
Le DG-STACK représente une alternative innovante aux problématiques auxquelles nos clients sont confrontés. Cette nouvelle solution s’inscrit parfaitement dans la philosophie dB & DEGREES qui vient d’obtenir le statut “Jeune Entreprise Innovante” !
N’hésitez pas à nous contacter pour en savoir plus sur cette solution ou solliciter notre expertise pour tous vos enjeux CEM & gestion thermique.