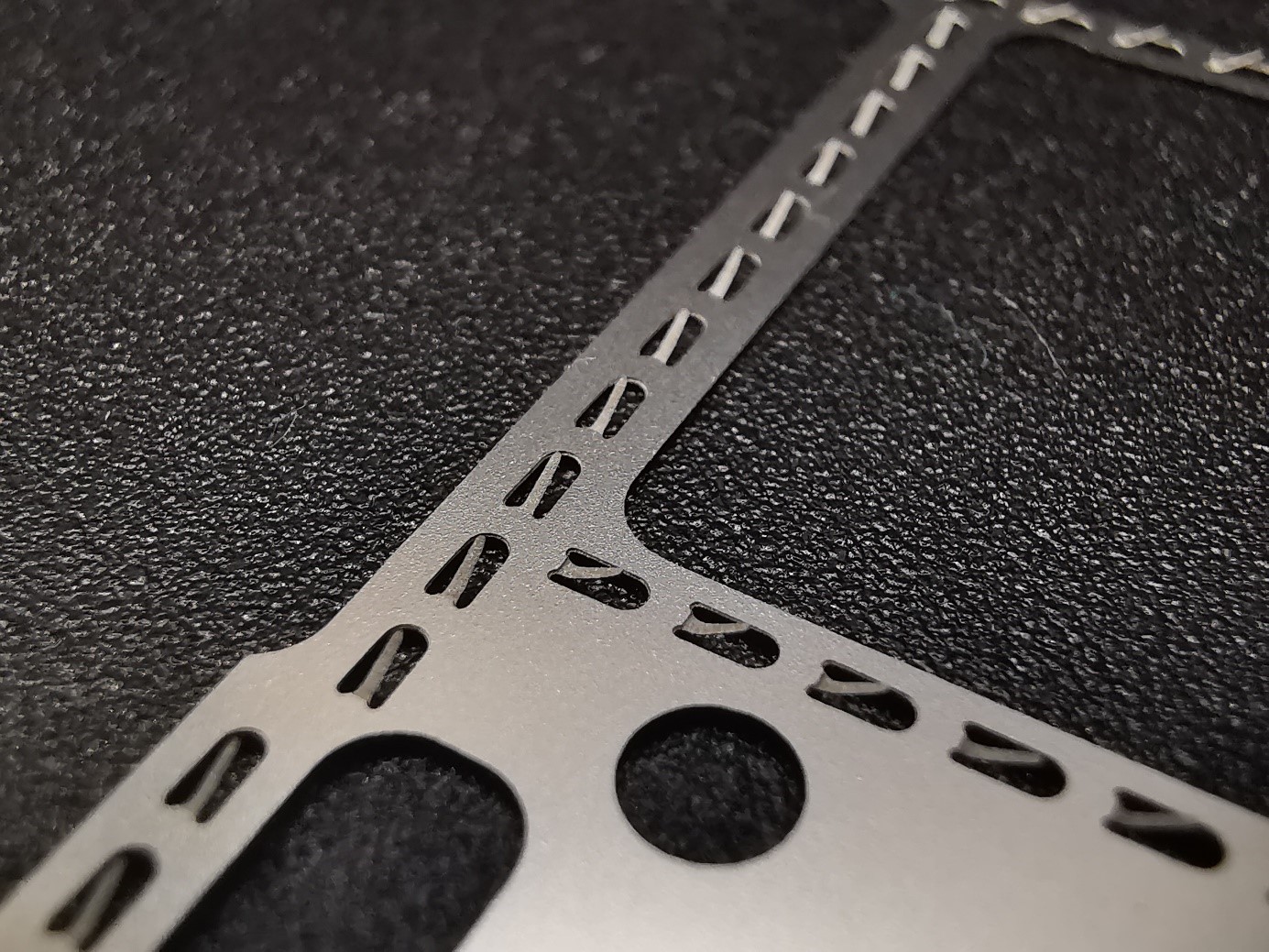
Publié le 19 décembre 2019
Pour limiter la susceptibilité et l’émission des interférences vis-à-vis des composants électroniques d’un circuit imprimé / PCB, le blindage électromagnétique du PCB nécessite un capot spécifique assemblé sur le circuit et doté généralement de plusieurs cavités. Ces cavités faradisent individuellement les différentes parties du circuit et globalement le PCB vis-à-vis de l’extérieur.
Mais la jonction entre ce capot multi-cavités et le circuit PCB n’est jamais parfaite (calcul des jeux/serrages/tolérances mécaniques), alors qu’elle est un élément essentiel pour assurer un blindage efficace = cette interface ne doit présenter aucune fente susceptible de laisser passer des signaux indésirés.
Un client du secteur des télécoms nous a récemment sollicités pour effectuer une réalisation de blindage électromagnétique sur une fonderie en aluminium.
Etude de cas d’utilisation d’un joint métal
Les solutions de contacts habituelles (serrage par vis, usinage des surfaces en contact….) avaient été explorées par ce client mais n’étaient pas envisageables pour des contraintes de coûts et d’encombrement mécanique :
- solidariser les deux éléments via un grand nombre de vis réduit l’espace disponible dans l’équipement, alourdit le poids de l’ensemble, et augmente son coût d’assemblage
- l’usinage est un procédé coûteux et peut s’avérer insuffisant pour un jointage satisfaisant
- le moulage-rectification est un procédé également coûteux et peut aussi s’avérer insuffisant
Le client envisageait alors de nous faire intervenir sur sa fonderie en aluminium pour y effectuer une dépose d’un joint FIP (FORM IN PLACE) conducteur électrique.
Sous une NDA (Non disclosure Agreement), il nous a confié ses plans 3D mécaniques et ses plans d’implantation PCB. Nous avons constaté que dans ce projet (application en bande K), les tolérances mécaniques exigées étaient un réel challenge technique qu’un joint traditionnel FIP ne pouvait pas garantir en phase série. Comme il n’y avait pas de contrainte d’étanchéité aux fluides (IP), nous avons alors préconisé une alternative au joint FIP : le joint métal.
Notre client était convaincu des nombreux avantages (techniques et économiques) et de la maturité du procédé : il avait déjà expérimenté cette technologie du joint métal dans le cadre de projets antérieurs pour le compte d’une autre société. L’intégrer à ce nouveau projet, très innovant et exigeant techniquement, s’avérait être le bon choix.
Les murs des cavités du capot ont pu être affinés et le nombre de vis a pu être réduit. Ces avantages techniques ont laissé encore plus de place au PCB.
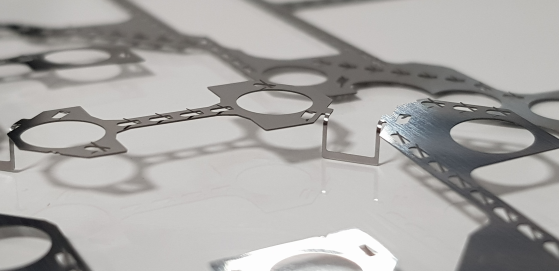
Nos valeurs ajoutées sur ce projet:
- conseil sur le choix des technologies les plus pertinentes pour répondre à leur problématique
- conception de l’architecture du joint pour s’intégrer entre la mécanique et le PCB (pontés, pinces, perçages….)
- étude de l’implantation et de la forme des ressorts en fonction des blindages attendus dans chacune des différentes cavités
- rapide modélisation 3D du joint métal pour une vérification de l’intégration du joint dans l’assemblage par le client
Le joint métal en résumé
Pour ce type de problématique, un joint métal peut s’avérer une très bonne solution. En effet les avantages du joint métal sont nombreux :
- Un faible encombrement dans l’épaisseur, de l’ordre de 0,15mm
- Une capacité de compensation de hauteur de 0,3mm à 1,6mm (si les ressorts sont pliés dans les 2 sens)
- Sur un même joint, il est possible de jouer sur les niveaux d’atténuations de blindage en modifiant localement les espacements des ressorts (pitch), et/ou en réalisant une double rangée de ressorts.
- On peut diminuer localement les épaisseurs des ressorts pour minimiser les efforts de compression
- C’est une pièce qui s’utilise autant sur des capots de blindage multi-cavités réalisés en plastique métallisé que sur des capots en métal
Epilogue
Notre client est à ce jour en phase de production série avec nos joints métal.
Notre collaboration en équipe se passe si bien que ses collègues nous sollicitent déjà sur un tout nouveau projet de télécom (en bande Q) qui utilisera certainement cette solution d’interfaçage.
Notez que si la solution adéquate avait été un joint FIP conducteur électrique, nous aurions tout aussi bien pu y répondre. Nous vous en parlerons d’ailleurs dans un prochain article !