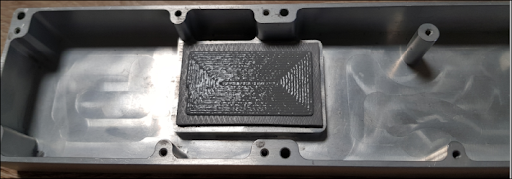
Posted on September 11, 2020
Most of the time, what comes as the ideal solution to fill this gap between the heatsink and the electronic components and thus promote the dissipation of the heat generated by the components, is the use of a thermal pad. To work properly, the thermal pad must be compressed, generally in the range of 15 to 40%. The compressive forces exerted on the thermal pad are directly undergone by the electronic board (PCB), which can go as far as generating a buckling of the PCB (mechanical deformation linked to an exerted force). This mechanical deformation of the PCB can lead to the desoldering of certain sensitive components, more precisely on BGA type ball components.
To limit this compressive force, while ensuring the thermal connection between components of different heights and a heat sink, it is possible to use thermal gels, also called thermal pastes or gap fillers. This solution consists in placing a thermally-conductive paste covering the hot components, in an amount sufficient to ensure mechanical contact with the heat sink. However, this method also has certain constraints. Indeed, the dispensing technique requires a specific machine which can be a costly investment.
In order to respond to this increasingly widespread problem, which neither of the two solutions fully satisfies, dB & DEGREES has designed an innovative product: the DG-STACK.
The principles of using the Thermal Pad
The Thermal Pad is a polymer loaded with heat transfer particles which, by compression, transfers heat from a hot source to a heat sink. The pads, more commonly known as thermal interfaces or mattresses, are dimensioned by its nominal thickness, YX dimensions, shore hardness, thermal conductivity and / or thermal resistance as well as the compression to be applied.
Most of the time, the integration in the mechanical assembly is done manually. As a general rule, a low-performing / low-thermal conductor material is flexible and easy to compress (1 to 5W/m.K), while higher-performing materials (6 to 32W/m.K) are often harder.
Benefits of the thermal pad
The advantages of the Thermal Pad are numerous:
- Easy to handle by hand
- Very low cost of cutting tooling when one tool is needed
- Good resistance to vibration
- Possibility of having one or two non-sticky sides
- Easy replacement in the event of maintenance
Disadvantages of the thermal pad
On thermally efficient pads, compressing the thermal pad requires significant mechanical efforts. These forces are then undergone by the electronic card (phenomenon of buckling). This can unsolder some fragile components, such as ball components for example. This is even more true on an electronic card having several components of different heights to be in contact with a common heatsink.
In this context, it will be necessary to provide several thicknesses of thermal pads (management of several item references), to compensate for all the differences in component heights and to ensure mechanical contacts with the heat sink without causing buckling of the electronic board. This diversity of thermal pads of different heights can, in certain cases, generate material losses during the cutting phase of the thermal pad sheet, and as a consequence, an increased production cost.
The principles of using the Gap Filler
Also called thermal paste, Gap Filler is a single or two-component pasty polymer material, which is deposited by an automatic device. It can also be deposited with a manual gun for simple reworks or small quantities in production. This material has the major advantage of being very easily compressible: it requires very little compression effort. The Gap Filler can fill spaces of up to 5 mm, be deposited on different heights of components arranged on the same card, cover a surface by depositing a bead of material or in blocks, etc.
Advantages of the gap filler
The pasty consistency of the material (similar to the toothpaste gel type) ensures a perfect thermal bond between the component and the heat sink with negligible compressive force. The paste can be deposited in different area on the card, in different thicknesses … from a single application program. The quantity of material to be deposited corresponds exclusively to the quantity required, which limits losses. The packaging in syringes, cartridges, or barrels makes it possible to adapt perfectly to production rates. In addition, the gap filler makes it possible to cover a very large range of mechanical tolerances min / max.
Disadvantages of the gap filler
When it is deposited by automaton, the gap filler requires an automatic depositing device (robot). When the paste is deposited by a subcontractor/EMS, and not on your own production line, this process requires complex logistics related to the dispatch of the mechanical parts (dissipators for example) on which the paste will be deposited. What is more, there may be some uncertainty as to the good resistance of the paste deposit during transport: in a vertical position for a prolonged period, the paste may have to slip slightly in certain contexts (shocks, vibrations, etc.). Finally, once deposited on the mechanism or on the electronic card, the gap filler cannot be handled directly by hand without altering its deposit geometry.
The unique dB & DEGREES solution: the DG-STACK
To respond to the problems of electronic boards buckling while solving the need for thermal dissipation, dB & DEGREES has developed the DG-STACK, a hybrid solution which consists in combining a gap filler deposit directly on a very thin thermal pad thickness.
(illustration depositing FIP on a material plate cut in 55x25mm/ depositing FIP of different heights on different shapes of pads in order to make a KIT).
Principle and use of DG-STACK
Thus, the manufacturer can continue to order thermal pads and deposit them manually, and with the DG-STACK, he will have benefited from the advantages of manually handling the thermal pad as well as the advantages of mechanical constraints of the gap filler. Appropriate packaging is then made to ensure transport in good conditions and easy grip of the part during integration into the equipment.
The DG-STACK applied directly to a mechanical part, will remain perfectly maintained on the metal surface thanks to the sticky nature of the thermal pad (TACKY) whatever its thickness. The gap filler deposited beforehand on the pad will be chemically attached and will thus be retained, limiting any risk of creep by gravity during transport, even in a vertical position and subjected to vibrations.
dB-STACK directly applied to a mechanical part
Whatever the geometry, it is therefore possible to implement this solution and thus ensure thermal continuity without exerting excessive pressure on your electronic components.
For each customer’s case, we take into account the gap to be filled and the mechanical tolerances sets of both the components and the mechanics to be placed in contact with these components. From this observation, we identify and adapt the necessary thermal pad height and the most suitable gap filler height. The solution is tailor-made, mechanically and thermally optimized, so as not to mechanically buckle the electronic board and not to damage either the electronic components or their soldering points on the electronic board, and to guarantee the good heat dissipation from the electronic components.
Our DG-STACK solution is available in two versions:
Thus, the DG-STACK allows us to offer a unique solution to ensure an optimal thermal connection with the heat sink. With this process, the gap filler will be distributed all around the components and will absorb the variations in height of each of them. Thanks to its properties, the gap filler will exert sufficient pressure on the thermal pad to ensure its compression and thermal efficiency. This innovative solution enables cutting-edge technology without the need for tools, machine investment and once-essential technical skills.
DG-STACK represents an innovative alternative to the issues our customers are facing. This new solution is perfectly in line with the dB & DEGREES philosophy which has just been awarded the “Young Innovative Company” status!
Do not hesitate to contact us to find out more about this solution or to seek our expertise for all your EMI & thermal management issues.